
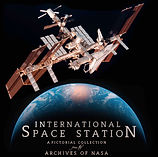
MANUFACTURING
As with any large scale international construction project, it has to be assembled in pieces as no single rocket can lift the entire ISS in one go. To do that, each module and component was built in parts around the world. This presented lots of engineering challenges.
The manufacturing processes to fabricate the International Space Station required the construction or modification of numerous factories around the world, and the recruitment of many companes and contractors to the project. To ensure quality operations in all manufacturing activities (despite the differences in language, measuring standards and politics), the International Organization for Standardization stepped in to supervise all technical details on behalf of the participating space agencies.
The ISS program called for the materials to be highly durable as it intended to last at least thirty years of space operations. This required certain metal alloys such as stainless steel, aluminum-vanadium alloy and titanium, and protective materials such as Kevlar, ceramic or carbon-fiber composite for micrometerioid shielding. Manufacturing processes involved press stamping, TIG welding, roll bending, laser cutting and many more activities.
The facilities involved in the massive international project stretched to almost every continent on Earth. When initial fabrication was completed, the station pieces were sent to a central factory at Kennedy Space Center for the last stages of manufacturing, outfitting and preparation for launch.
Marshall Space Flight Center
In Huntsville Alabama is a huge complex of buildings for NASA's advanced spacecraft propulsion and systems development. It was operational during the Apollo era, and served as a manufacturer of the Quest airlock, parts of Node 1 and the US laboratory. MSFC has another campus in New Orleans that contributed to the fabrication of American elements of the ISS.
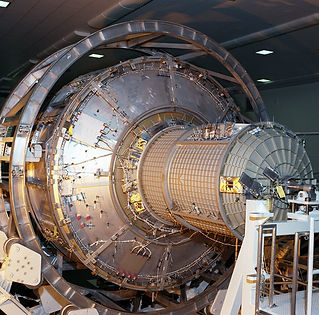
Boeing and Lockheed Martin facilities
NASA's first and oldest contractor - Boeing, manufactured steel and titanium girders for the S0 truss at their factory in the Los Ageles Metropolitan Area (specifically Huntington Beach, CA). Other parts fabricated by Boeing and Lockheed Martin tenants in New Orleans' Michoud Facility also ended up here.

Tsukuba Space Center
The Japan Aerospace eXploration Agency (JAXA) manufactured their Kibo "Hope" module at their Tsukuba Space Center (located in Ibaraki Prefecture, 100 km from Tokyo).

Michoud Assembly Facility
As part of Marshall's external campus in New Orleans, the Michoud Assembly Facility is a complex of production buildings that fabricated parts of the Solar Arrays, Truss and Radiator sections and the US laboratory module. They were sent to Marshall in Alabama for testing before heading to the SSPF in Florida.

Thales Alenia Space Corp.
One of the European Space Agency's prime factories for their modules is located in Turin, Italy, operated by Thales Alenia Space Corp. They manufactured the structural shells of Node 2, Node 3 and the Cupola.
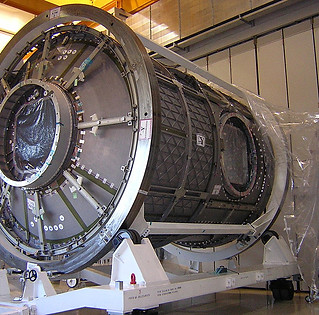
ESA ESTEC and EADS
ESA's larest ISS science contribution - the Columbus laboratory, was initially manufactured at Airbus' space factory in Germany, and tested it at ESTEC in the Netherlands before flying to the SSPF for last stages of manufacturing.

Construction
Materials



Carbon Steel
Chromium
Aluminium-titanium alloy
Copper
Stainless steel
The
Space Station
Processing Facility
At the Kennedy Space Center industrial area is a remarkable factory building that served as the prime facility for prefabricated ISS components to complete manufacturing activities, assembly of parts, fitting and installation of cables and machines, and launch processing operations. It is their last stop on Earth before hitching a ride in the shuttle to orbit.
Built in 1991 and completed three years later, the SSPF is the world's largest climate-controlled single chamber cleanroom factory, with an internal volume of 111,888 cubic metres.